振動切削技術(shù)的優(yōu)點(diǎn)有哪些?
振動切削技術(shù)具有以下優(yōu)點(diǎn):
### 一、改善切削力特性
1. **減小平均切削力**
- 在振動切削中,刀具與工件之間的相對運(yùn)動是周期性變化的。當(dāng)?shù)毒咴谡駝拥姆蛛x階段(刀具與工件脫離接觸)時,切削力降為零。這種周期性的切削力變化使得平均切削力減小。例如,在車削加工中,傳統(tǒng)切削方式下的主切削力可能為1000N,而采用振動切削技術(shù)后,平均主切削力可能降低到600N左右。這對于加工薄壁零件或細(xì)長軸類零件尤為重要,因?yàn)檩^小的切削力可以減少工件的變形,提高加工精度。
2. **抑制切削力波動**
- 與普通切削過程中可能因積屑瘤、刀具磨損等因素引起的切削力波動不同,振動切削的切削力波動是有規(guī)律的。通過合理設(shè)置振動參數(shù)(如振動頻率、振幅等),可以將切削力波動控制在一定范圍內(nèi),使切削過程更加穩(wěn)定。例如,在銑削加工中,由于振動切削力的規(guī)律波動,銑削過程中的振動幅度減小,加工表面的質(zhì)量得以提高。
### 二、提高加工表面質(zhì)量
1. **減小表面粗糙度**
- 振動切削時,刀具的振動使得切屑的形成方式發(fā)生改變。切屑在振動作用下更容易斷裂成細(xì)小的碎片,而不是連續(xù)的長切屑。這種細(xì)小的切屑在排出過程中對已加工表面的劃傷作用較小。同時,由于切削力的減小,刀具對工件表面的擠壓和摩擦也減小,從而使加工表面粗糙度降低。例如,在車削外圓時,傳統(tǒng)切削方式下表面粗糙度\(Ra\)值可能為3.2μm,采用振動切削后,\(Ra\)值可降低到1.6μm以下。
2. **改善表面完整性**
- 振動切削能夠減小工件表面層的殘余應(yīng)力。在普通切削中,刀具對工件的切削力和切削熱會使工件表面層產(chǎn)生較大的殘余應(yīng)力,影響工件的疲勞強(qiáng)度等性能。而振動切削由于切削力和切削熱的減小,表面層的殘余應(yīng)力也相應(yīng)減小,并且表面層的微觀組織變形也得到改善,提高了表面完整性。
### 三、延長刀具壽命
1. **減小刀具磨損**
- 振動切削過程中,刀具與工件之間的間歇性接觸減輕了刀具的磨損。在分離階段,刀具得到冷卻和潤滑,減少了刀具因高溫和摩擦導(dǎo)致的磨損。例如,在鉆削加工中,采用振動切削技術(shù)的鉆頭相比傳統(tǒng)鉆削,其磨損速度明顯減慢,刀具壽命可延長30% - 50%。
2. **抑制刀具破損**
- 由于振動切削減小了切削力和切削力的波動,刀具在切削過程中受到的沖擊力也減小。這有助于抑制刀具的破損,特別是在加工高硬度材料或進(jìn)行斷續(xù)切削時,振動切削能夠有效地保護(hù)刀具,降低刀具破損的風(fēng)險(xiǎn)。
### 四、提高加工精度
1. **尺寸精度**
- 如前文所述,振動切削減小了切削力,從而減少了工件在加工過程中的彈性變形。這使得加工后的工件尺寸更加接近設(shè)計(jì)尺寸,提高了尺寸精度。例如,在銑削精密零件時,采用振動切削技術(shù)可以將尺寸精度控制在±0.01mm以內(nèi)。
2. **形狀精度**
- 對于形狀復(fù)雜的工件,振動切削的穩(wěn)定切削力和良好的切屑控制有助于提高形狀精度。在加工曲面零件時,由于振動切削可以有效抑制切削力波動引起的刀具偏移,能夠加工出形狀更加精確的曲面,減少形狀誤差。
東莞京雕教育擁有自己的實(shí)體工廠,各種數(shù)控設(shè)備70余臺,近萬平米的教學(xué)場地,20年行業(yè)經(jīng)驗(yàn),開設(shè)CNC數(shù)控技術(shù)班、UG編程班、北京精雕班、車銑復(fù)合班、五軸編程調(diào)機(jī)班、浮雕、吸塑、滴塑技術(shù)班等,學(xué)會為止安排工作。
我們的培訓(xùn)模式是產(chǎn)教融合的模式,現(xiàn)有廠地上萬平米,擁有70多臺各種數(shù)控設(shè)備,包括三菱、發(fā)那科、新代、北京精雕、車銑復(fù)合、五軸機(jī)等先進(jìn)設(shè)備,讓學(xué)員能夠在實(shí)操練習(xí)中獲得更多的技能和經(jīng)驗(yàn)。
我們的使命是:讓更多的年輕人學(xué)到一技之長,讓更多的年輕人生活越來越幸福。
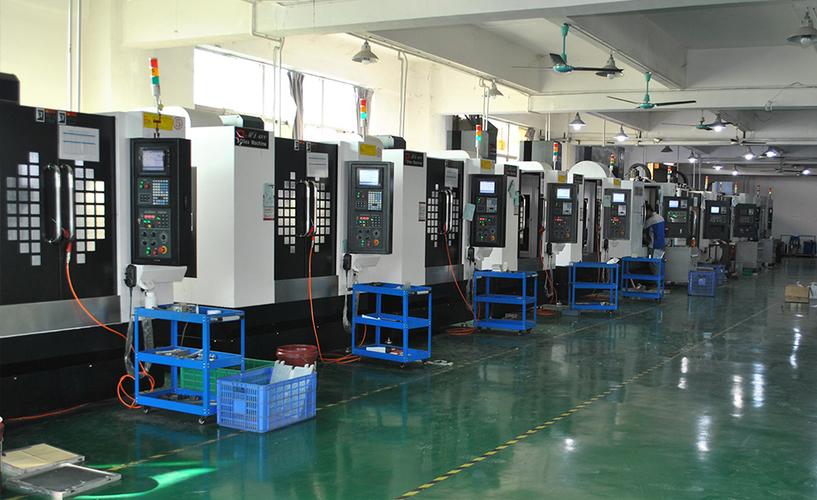